- 70% faster and 30% less expensive than alternative construction methods
- Studios are printed in one day, delivered & installed within a week
- $9M+ in Revenue since 2020
- Delivery of the first Azure Studios began in May 2023
- Previous Republic CF raise of $598k helped fund the first production line
- Revolutionizing the construction industry by 3D printing recycled materials
- 70% faster and 30% less expensive than alternative construction methods
- Studios are printed in one day, delivered & installed within a week
- More efficient & sustainable than other 3D printing construction technology
- $5.2MM in signed Purchase Orders and $22.1MM in Pre-Orders
- Delivery of the first Azure Studios began in May 2023
- Previous Republic raise of $598k helped fund the first production line
Traditional housing construction is slow and unsustainable- Housing shortage
There is a global shortage of housing. The United States alone needs an estimated 5.24 million housing units, and that number has been growing. - Archaic building methods
The construction industry relies upon outdated methods and materials, delivered by a labor force in increasingly short supply. Traditional solutions have been unsustainable. - Environmental impacts
The construction sector is the largest global consumer of raw materials and is responsible for about 11% of the world's total carbon emissions. Building homes have far too much of a negative environmental impact.
3D printing entire structures using recycled plasticAzure is fundamentally changing the construction industry by leveraging 3D printing technology using recycled polymers to prefabricate modern backyard studios, ADUs and homes faster and more affordably than ever before. Azure homes are printed in 70% less time and are 30% less expensive than alternative building methods—automating and accelerating production to meet urgent housing demands.
Fabrication takes place in the Azure factory, improving precision & quality. The controlled environment allows Azure to deliver projects faster than has been previously possible. The 3D manufacturing process and the additive material used will meet California and International Residential Codes.
Innovative construction: Fast, durable, & sustainable— The Print MaterialThe primary component of our print material is recycled polymer, a material predominantly used for food and drink containers.
The print material produces several desirable properties such as insulation, water resistance, printability, strength, stiffness & impact resistance creating a durable and reliable structure. — The StructureThe unique structural & print design creates a complete structure that is monolithically printed — further enhancing the ultimate strength of the composition. Additionally, the geometric designs of the floor, walls, and roof have been optimized & tailored to simplify all subsequent finishings. The PrintThe self-supporting structure of each Azure module is printed in less than 24 hours.
The PrefabricationOur printed structures are completed with installations of: - Doors and glass windows
- Internal MEP (mechanical, electrical, and plumbing)
- Interior flooring, wall and ceiling finishings
- Bathrooms & Kitchen for ADUs and Homes
— The DeliveryIn advance of the scheduled delivery date, the site foundation and utilities are completed and ready to receive the delivery of single or multiple printed modules. Modules are delivered on a flatbed truck, craned or forklifted onto the foundation & connected to live site utilities. 40+ units built to dateFocused on scalable ADU construction in 2023Since 2019, we have invested over $1,000,000 into engineering and research to design a process for 3D printing homes using recycled materials. While designing the new method, we completed over 40 houses, ADUs, and backyard studios—increasing revenue by 195% from 2019 to 2020, and by 260% from 2020 to 2021. Since launching our website in early January 2022, we have received paid pre-order deposits for units valued at over $25,000,000. We start with backyard studios, as their 120 sq ft size means that, in general, planning permission not required. Avoiding potential bureaucratic red tape delays will allow us to produce & install at a fast pace. 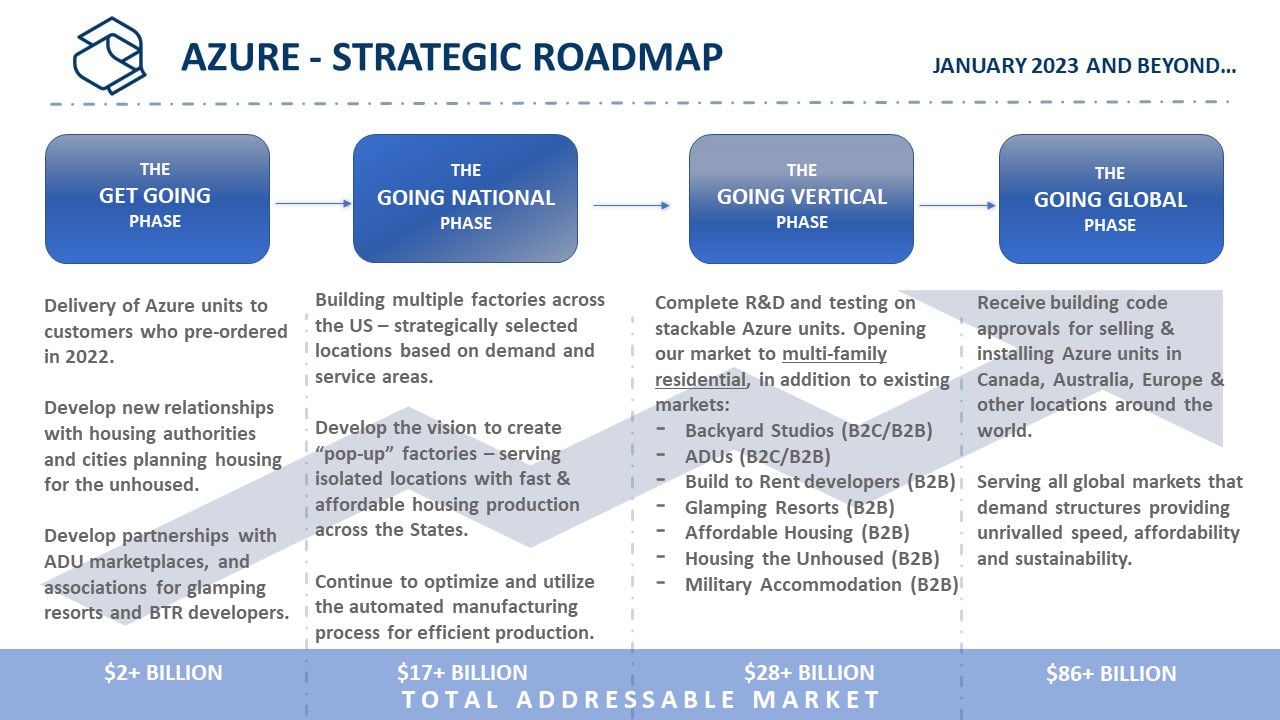
As the first 3D printed structure printed from recycled materials, we've made (and continue to make) more than our fair share of headlines, appearing in over 100 publications in four languages. All publicity has been organic—no PR agency or paid placements. 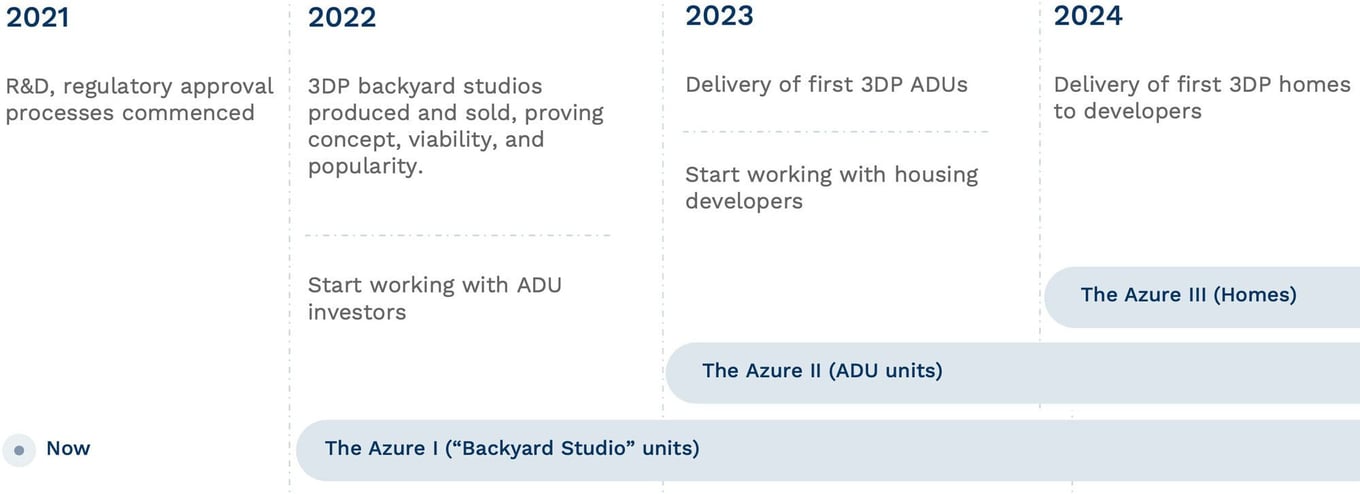
Developers, Housing Authorities and Homeowners Azure is a B2B business and B2C business. We are selling Backyard Studios and ADUs directly to homeowners, investors & glamping resorts; while we sell homes to developers and housing authorities. —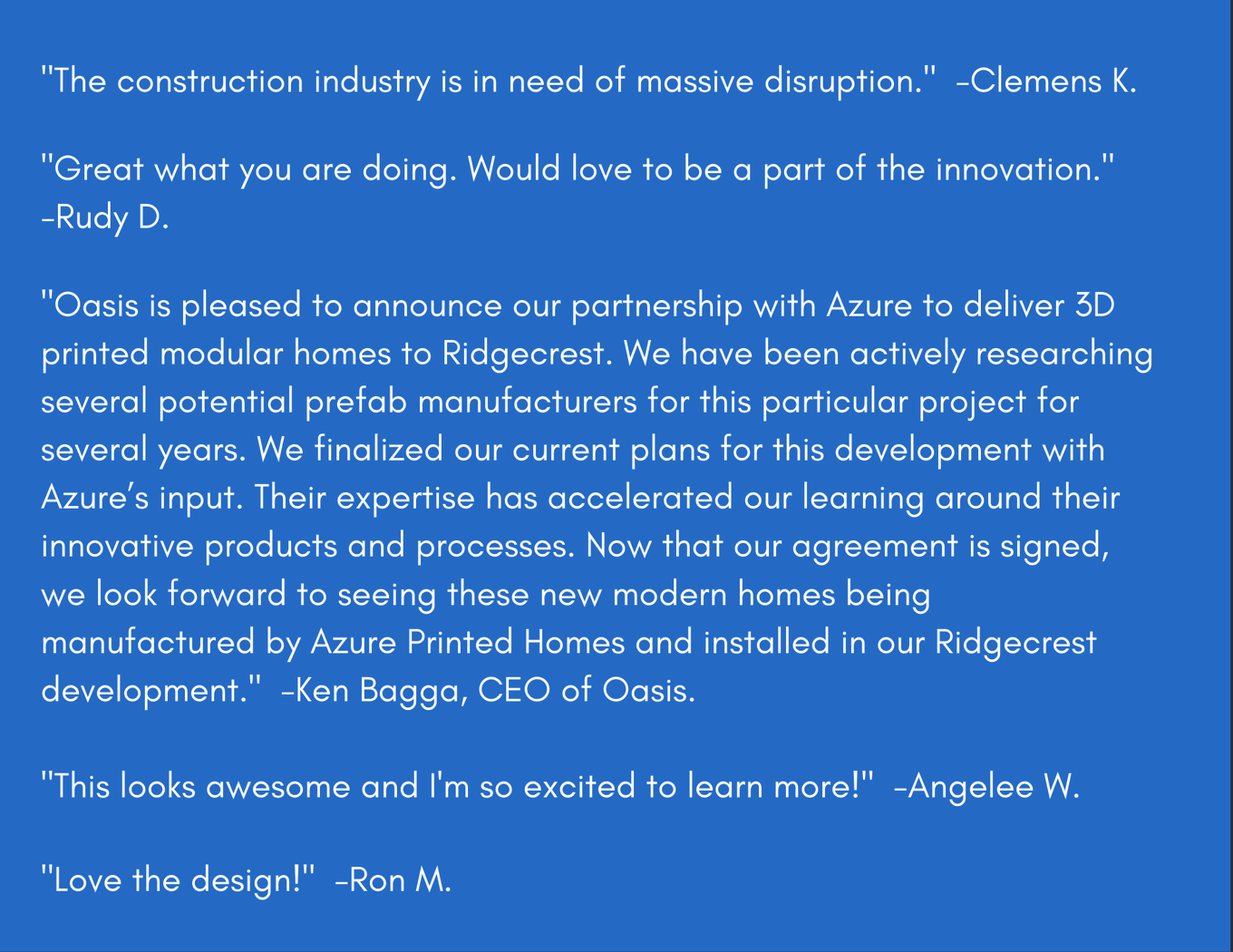
Strong unit economicsOur gross margins are 35%. We collect a small pre-order deposit, 10% of the purchase price upon receiving the order, and the balance before the units are shipped. Customers generally pay in cash or arrange their funding; however, Azure also offers a finance program through a financial partner. Why now- With more homeowners working from home during and after COVID, there is a high demand for backyard studios and ADUs.
- New materials and faster 3D printers are unlocking new construction methods that are fundamentally changing the industry.
- New government regulations are helping to facilitate faster permit approvals.
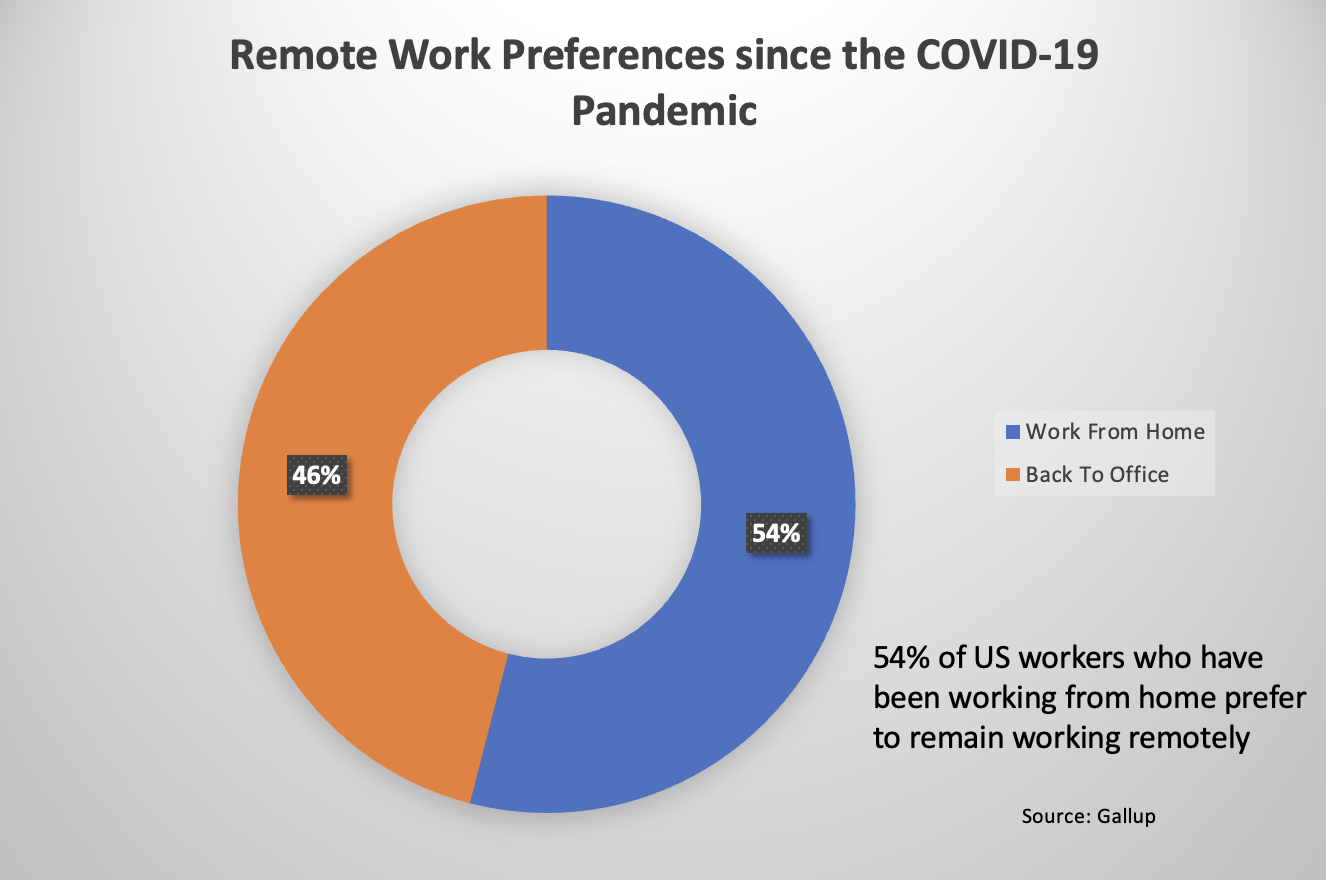
— Market size & segments
- Backyard Studios
Sheds & Backyard Structures are a $6B industry. The ongoing pandemic and remote-work policies have accelerated the Working from Home (WFH) trend, increasing demand for backyard offices.
- ADUs
Low-cost, implementable approach to infill development. Suited to high-cost cities with little vacant land and abundance of low-density development. $1.8B business in California alone.
… Read moreHow is Azure different from other 3D Printing companies?None of our competitors have capitalized on the true benefit of 3D Printing: its efficiency and mass production. Competitors are: The Azure Printed Home moves beyond existing printing options in the construction industry, by enhancing: - Sustainability - print material and through product life
- Material design efficiency - structural, waterproofing, light-weight & transportable
- Production speed - full module shell print, unaffected by weather conditions
- Production cost - efficiency of inclusive roof and floor print
- Regulatory
… Read more
A better way to build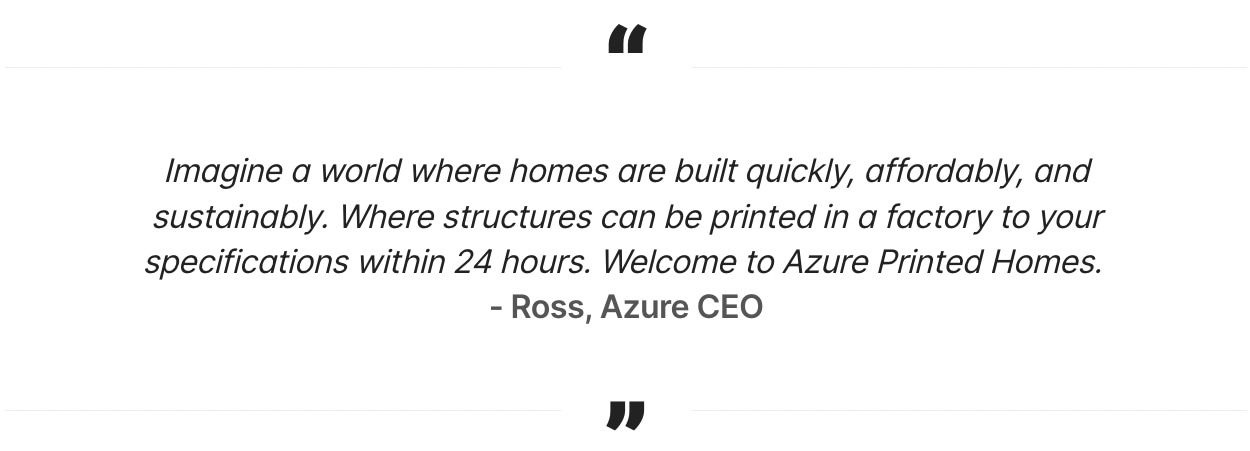
Azure Printed Homes is disrupting the construction industry by changing the way homes are built. We have a vision where construction projects are built quickly and more affordably while also repurposing existing building materials and cutting emissions instead of having to utilize new resources. We are ready to take on partners to bring this idea to the next level: a starter production facility generated $4 million* in revenue for the company in 2022, and projected approximately $20 million* in 2023 when the plant is fully operational. In the future years, we will open similar factories in other states growing Azure to become one of the major prefab manufacturers. 
Addressing the construction industry's sustainability problemThe production of traditional construction materials such as concrete contributes to about 11% of the world's carbon dioxide (CO2) emissions. Our printed material takes an abundant universal waste product, in plastic, and transforms it into a structurally-responsible polymer that we can 3D print. We see this as a stepping stone toward a more fundamental use of recycled plastic and 3D printing in the home building industry. Beginning as a bootstrapped startupAzure Printed Homes has been completely self-funded to date with an internal investment of approximately $1,000,000. Now we want to crowdsource this business, not just crowdfund it. Therefore, despite being told that we could raise at a much higher valuation, we chose to price this round conservatively under 6x our current revenue run rate. We chose this for two reasons. First, we want our earliest supporters to get a great deal so that they feel valued and are appropriately rewarded for believing in us. The second is that our executive team has been around the block, and we've seen what happens when entrepreneurs over-value their companies—creating many problems down the line for future financings or exits. So we aim to set the stage for the best possible outcomes by pricing conservatively—for everyone involved. We're staunch believers that companies should only raise money if they firmly committed to delivering a return for their investors. Of course, we can't predict the future, but our management team now works for YOU—and we will work tirelessly to get you the best return on your investment. We're raising on Republic because we want all our fans and early adopters also to have an opportunity to be investors and co-owners. 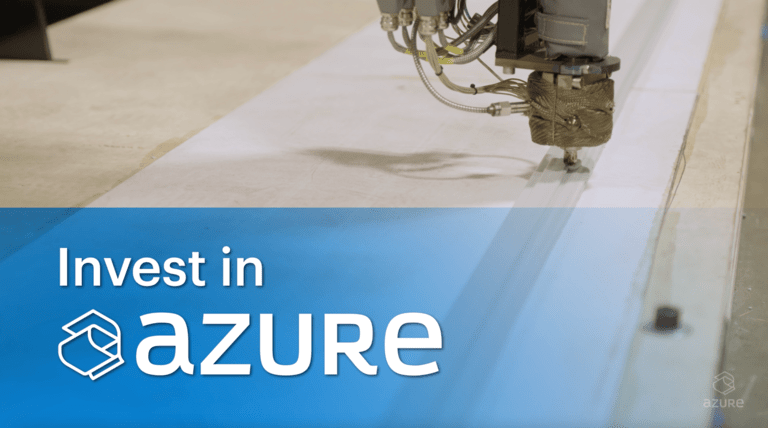
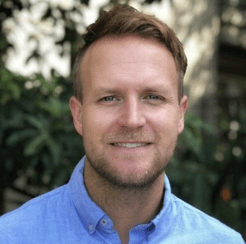
Ross Maguire- MS Civil Engineering, 13 years experience in construction, design and project management
- Founded and led his own residential & commercial construction company in London, UK for 8 years
Yuri Eidelman
- 35 years of experience as a Licensed California General Contractor
- Cofounded three start-ups in different industries, with exits through sales to private and public companies
.jpg) |
Коментари
Постави коментар